The Top Methods for Aluminum Casting That You Required to Know
From the standard sand spreading technique to the elaborate investment casting procedure, each strategy offers distinct advantages that provide to various job demands. As we navigate via the top techniques for light weight aluminum spreading, it ends up being apparent that mastering these approaches is critical for attaining optimum results.
Sand Casting Strategy
The Sand Spreading Method is a fundamental approach in light weight aluminum casting, commonly used for its cost-effectiveness and versatility in developing complex metal forms. This method involves producing a mold made of compressed sand into which liquified aluminum is put, enabling it to solidify and take the shape of the mold. Among the key benefits of sand casting is its capacity to create complicated geometries with relatively reduced tooling expenses, making it an eye-catching option for producers seeking to create one-of-a-kind parts.
In the sand casting procedure, a pattern of the final component is pressed into a great sand mix included within a flask. As soon as the pattern is removed, a dental caries representing the last component's shape is left in the sand. Molten light weight aluminum is after that put into the dental caries, filling up the room and taking on the specific details of the pattern. After the light weight aluminum solidifies and cools down, the sand mold and mildew is escaped, exposing the freshly cast light weight aluminum part. Sand spreading is frequently made use of in various markets, consisting of auto, aerospace, and art foundries, because of its capacity to create both little and big steel parts with elaborate styles.

Investment Casting Refine
A complex method used in aluminum spreading is the Investment Casting Refine, understood for its capacity to create very outlined and intricate steel components. Referred to as the lost-wax casting process, this strategy dates back thousands of years and remains a prominent choice in different sectors due to its flexibility and accuracy.
The financial investment casting procedure starts with the creation of a wax pattern, which is coated with a ceramic covering to create a mold. The wax is after that thawed out, leaving a cavity in the shape of the preferred component. Molten aluminum is poured into the ceramic mold, taking and loading the cavity on the elaborate information of the initial wax pattern.
This approach is preferred for its ability to produce complicated forms with superb surface finish and dimensional accuracy. It is frequently made use of in the production of aerospace elements, precious jewelry, and commercial equipment where intricate designs are needed. The investment casting procedure supplies high repeatability and can generate components with minimal machining required, making it an affordable option for lots of applications.
Irreversible Mold And Mildew Approach
Using a various method from the Investment Casting Refine, the Permanent Mold Method in aluminum spreading offers a distinctive strategy for producing metal elements. The warm transfer from the molten steel to the mold aids in strengthening the aluminum promptly, lowering the cooling time contrasted to sand casting.
One of the vital advantages of the Permanent Mold And Mildew Method is the boosted surface area coating and dimensional accuracy of the spreadings created. This method is additionally known for its capacity to create high-strength light weight aluminum elements with constant quality. In addition, the recyclable nature of the mold and mildew makes it an economical option for tool to high volume manufacturing runs.
Pass Away Casting Innovation
Utilizing sophisticated production processes, die casting innovation provides a highly effective technique for generating intricate aluminum elements. This strategy entails infusing liquified aluminum into a steel mold and mildew, called a die, at high stress. The die is specially developed to form the light weight aluminum right into the wanted form, resulting in high precision and exceptional surface area coating.
Pass away casting deals numerous benefits. It permits the manufacturing of intricate forms with slim wall surfaces, limited tolerances, and smooth surfaces, making it perfect for applications where looks and accuracy are essential. Additionally, die casting enables rapid production rates, reducing overall production time and costs.
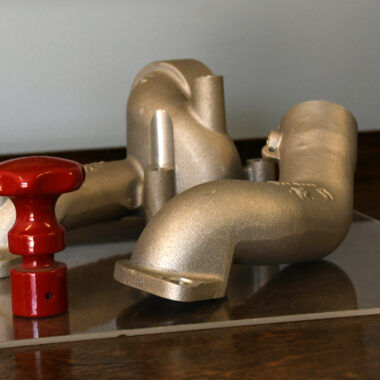
Lost Foam Casting Method
Die casting innovation's effectiveness and precision in creating aluminum elements lead the means for discovering the Lost Foam Spreading Technique as a corresponding production method. Lost Foam Casting, likewise known as evaporative pattern spreading, is an approach that utilizes foam patterns to produce elaborate visit homepage aluminum components.
Among the crucial advantages of Lost Foam Casting is its capacity to produce complex designs with detailed information that may be challenging to attain via standard casting methods. Additionally, this strategy gets rid of the need for cores, reduces machining procedures, and enables tighter resistances. Lost Foam Spreading is particularly ideal for little to medium-sized aluminum components that need high precision and detailed geometries. aluminum casting. As markets continue to require lightweight yet durable elements, Lost Foam Casting confirms to be a useful method in the world of aluminum spreading.
Conclusion
In final thought, understanding the top strategies for aluminum casting is important for achieving top notch cause the manufacturing process. Sand spreading, investment casting, long-term mold and mildew, pass away spreading, and lost foam casting are all reliable methods for producing light weight aluminum components with various levels of complexity. By understanding these techniques, makers can make certain that their products meet the preferred requirements and criteria for performance and resilience.
From the standard sand casting technique to the complex financial investment spreading procedure, each strategy offers distinct advantages that cater to different task needs.The Sand Spreading Technique is a fundamental method in light weight aluminum spreading, extensively utilized for its cost-effectiveness and versatility in creating detailed metal shapes. Lost Foam Spreading, additionally recognized as evaporative pattern spreading, is an approach that makes look at here use of foam patterns to develop detailed light weight aluminum parts. As industries proceed to require light-weight yet long lasting elements, Lost Foam Casting shows to be an important method in the world of aluminum spreading.
Sand spreading, financial investment casting, permanent mold, pass away spreading, and lost foam casting are all efficient techniques for producing aluminum components with various levels of complexity.